ANTI-PUNCHING ARMOR REINFORCEMENTS
The weight of a plate supported on a column induces shear stresses on the slab. These stresses, if sufficient and where no additional reinforcement is provided, would result in the ‘drilling’ column through the slab. This perforation cut is similarly induced at the base on which the column rests. Although the drilling cut can be alleviated by the localized thickening of the cement with the supporting beams and extended column heads, the construction of flat plates offers many advantages. A consistent main space can reduce the total height of a building to 3 and can provide significant time and material savings.
Typical arrangements
Our Shearfix system is suitable for all speaker shapes and locations. The layout of the Shearfix rails is determined by the design calculation or design program. Some of the typical arrangements are shown here.
The weight of a support slab on a column induces shear stresses in the slab. These stresses are sufficient, when additional reinforcement is not foreseen, result in “perforation” by the column through the slab. This perforation effect is also induced at the base of the column. Although the punching can be alleviated by localized thickening of the cement with hanging beams and attenuated by capitals protruding from the pillars, the construction of flat slabs offers many advantages. Cortartec Shearfix is the ideal solution for the design and construction of problems associated with punching. The system consists of connectors with two heads welded to flat bars and are positioned around the top of the column or at the base. The cutting force of the slab is transferred through the connectors into the column. The connectors are welded to the rail at specific centers or when calculating the design. Cortartec Shearfix is suitable for all forms of columns and it is very easy to install the ‘top down’ or ‘bottom up’, depending on the preference on site.
Radial Layouts
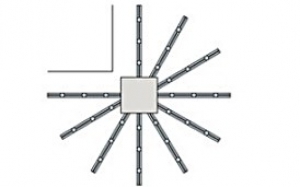
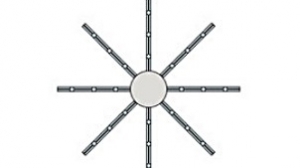
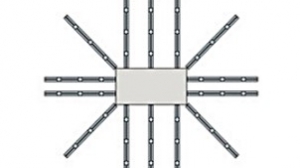
Cruciform Layouts
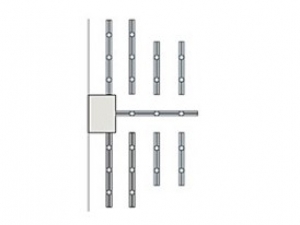
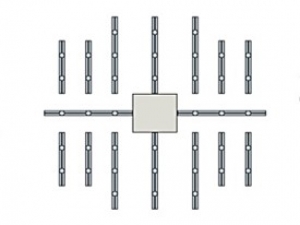
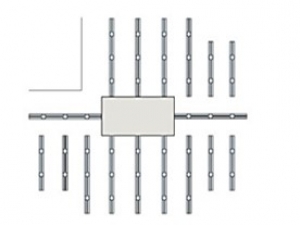
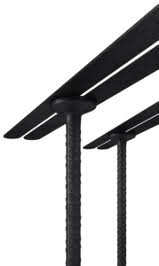
Sizes / Settings
The Shearfix system consists of double-headed spikes welded to flat rails. It is manufactured to meet the specific needs of each application. The screws are manufactured in five diameters (10, 12, 16, 20 and 25mm) of reinforcement bar approved by CARES B500C. The heads are hot forged to three times the bar diameter. Screws are manufactured in almost any length to suit the depth of the slab, but are usually formed in 5mm increments within the 100-1000mm range. The bar used in this system has a characteristic elastic limit of 500N / mm2. The pins are welded to the rail at the centers determined by the design calculation. Shearfix rails are manufactured from steel strips, 16mm wide x 3mm thick on screws up to 16mm in diameter and 20mmx5mm on the two bolt diameters. The rails have rounded ends to reduce the risk of injury during handling. The space between the strips allows the passage of concrete during casting and also allows the rail to allow the rail to be nailed through spacers to the formwork when fixed ‘from the bottom up’, that is, before any other reinforcement.