GK profiles, with their design and form of presentation, offer an unusual assembly speed for a stainless steel profile system, obtaining lower installation costs than any other system, all without giving up a perfect, stable and durable over time, absorbing lining and wind loads and meeting all established safety factors.
The systems consist of a set of vertical profiles that are anchored to the slabs or walls by means of leveling supports, freeing the walls from the support function. Fixing anchors are fixed, which in turn support and transport the efforts of the
cladding plates to profiles.
As a basic rule of installation, profiles should be anchored to the floors of each floor. Intermediate anchors must also be applied to masonry. If it is not possible to anchor the profile at both ends of the slabs, it must at least be anchored to one of the floor slabs.
The entire system results in a flat cladding surface between 4 and 15cm away from the top of the floor slabs and / or the inner wall.
Fixing to the floor must be done by means of expansion screws, or, if this is not possible, by means of a chemical fixation composed of threaded rod in stainless steel and epoxy resin.
Every six meters of profile placed, a minimum 20mm joint should be left between the profiles to accommodate expansion movements.
The leveling brackets are fixed to the profile with screws.
At intermediate support points, it is recommended to use retaining brackets fixed to the profile using self-tapping screws. The retaining brackets have a vertical slot that allows the system to absorb differences resulting from expansion, as well as possible movements of the floor slabs due to the laying of the building.
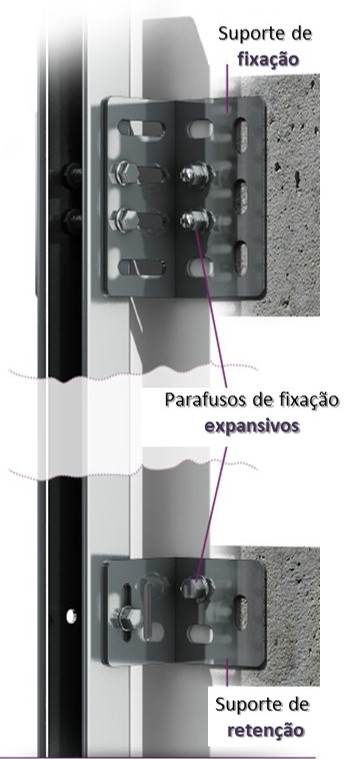
The Gk profile clamping system has several advantages over point clamping methods:
Fast execution: thanks to the use of profiles, assembly costs are reduced.
• Aesthetics: the possibility to choose various materials and of different dimensions.
• Lightness of the system in the coating.
• Ease of installation, regardless of weather conditions.
• Low maintenance.
• Excellent stability of the coating, without risk of cracks or displacements due to the breakdown of the coating plates.
• High thermal insulation, thermal bridges are eliminated.
Absence of perforations in the masonry walls.
• Improved sound insulation.
• Perfect planimetry of the facade.
• Eliminates moisture condensation.
• Cleaning of the elements: the use of mortar is eliminated.
• Safety: the profiles are fixed directly to the floor, the transmission of loads from plate to plate is eliminated, as the fixings are independent.
• Fast fixing and adjustment of anchors to the profile, thanks to its innovative anchoring system.
• Creation of a space between the cladding and the wall, to accommodate technical installations.
Vertical “U” profile system
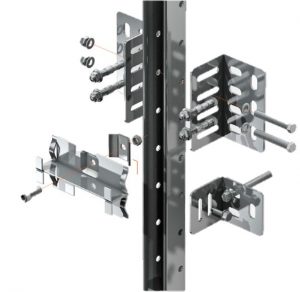
System of vertical U-profiles in stainless steel. Profiles are supplied cut to size
and machined at the points where they are to be attached to the supports.
The anchors are fixed to the profile by a clamping system, consisting of a set of screws with nut and a clamping washer. Once the set of anchors has been placed, it slides along the profile, facilitating its movement to the position where it must be fixed. Depending on the tightening torque, the maximum weight allowed before the anchor slips is determined in the anchor load table. For safety, it is recommended to always apply the maximum tightening torque (16.5mm) allowed by the screw.
Omega OR profile system
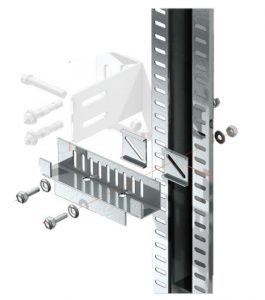
System of vertical perforated profiles in the shape of Omega. Rigorous dimensions through quality control.
Drilling d0 torn holes of model spacing in the flaps allows to mark a screw or fixing step to the profile. In turn, the vertical grooves of the anchoring clip, together with the incorporation of a non-slip washer, allow it to be fixed to the profile, achieving adjustments in any position.
Omega OP Profile System
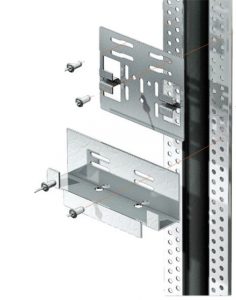
New vertical drilling system for Omega profiles. At the factory, and through an industrial and rigorous process, the flaps of the Omega OP profile are perforated.
Modular drilling with stepped holes allows you to easily mark the fixation of the profile. At the same time, the torn holes in the anchors multiply the possible joining positions between the anchoring and the profile, achieving millimeter adjustments.
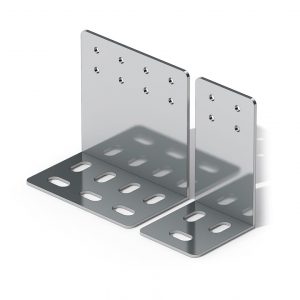
Support bracket
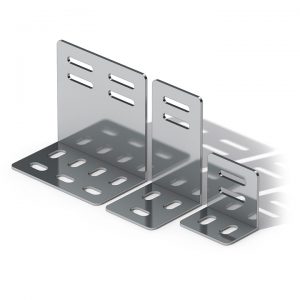
Fixing bracket
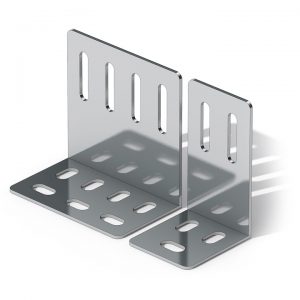
Leveling square
Tuning brackets
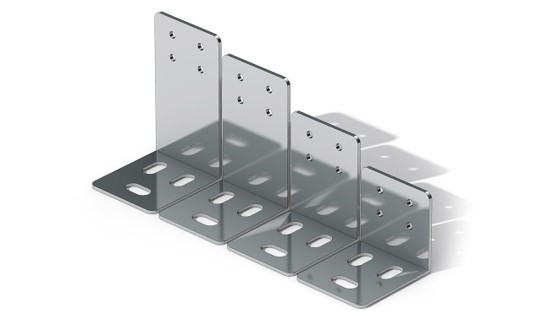
Manufactured in stainless steel (AISI 304/316, according to specifications EN 10088-1 and EN 10088-2), fixed to the structure and / or masonry.
When used as load supports, they transmit the vertical loads of the facade directly to the slabs, being fixed by means of mechanical anchors. When used as intermediate supports, they prevent the profile from flexing due to the effect of the wind and are fixed with screws with nylon bushing and / or chemical bushes.
Its design makes fixing and leveling profiles on the job a very quick and simple task.
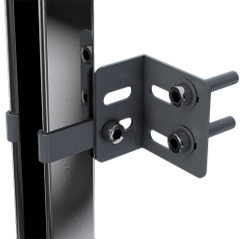
Auxiliary profile support
Made of stainless steel (AISI 304/316, according to the specifications EN 10088-1 and EN 10088-2), they are used to fix and support the profile in areas where there are no perforations.